The Comprehensive Guide to Plastic Molding Manufacturing
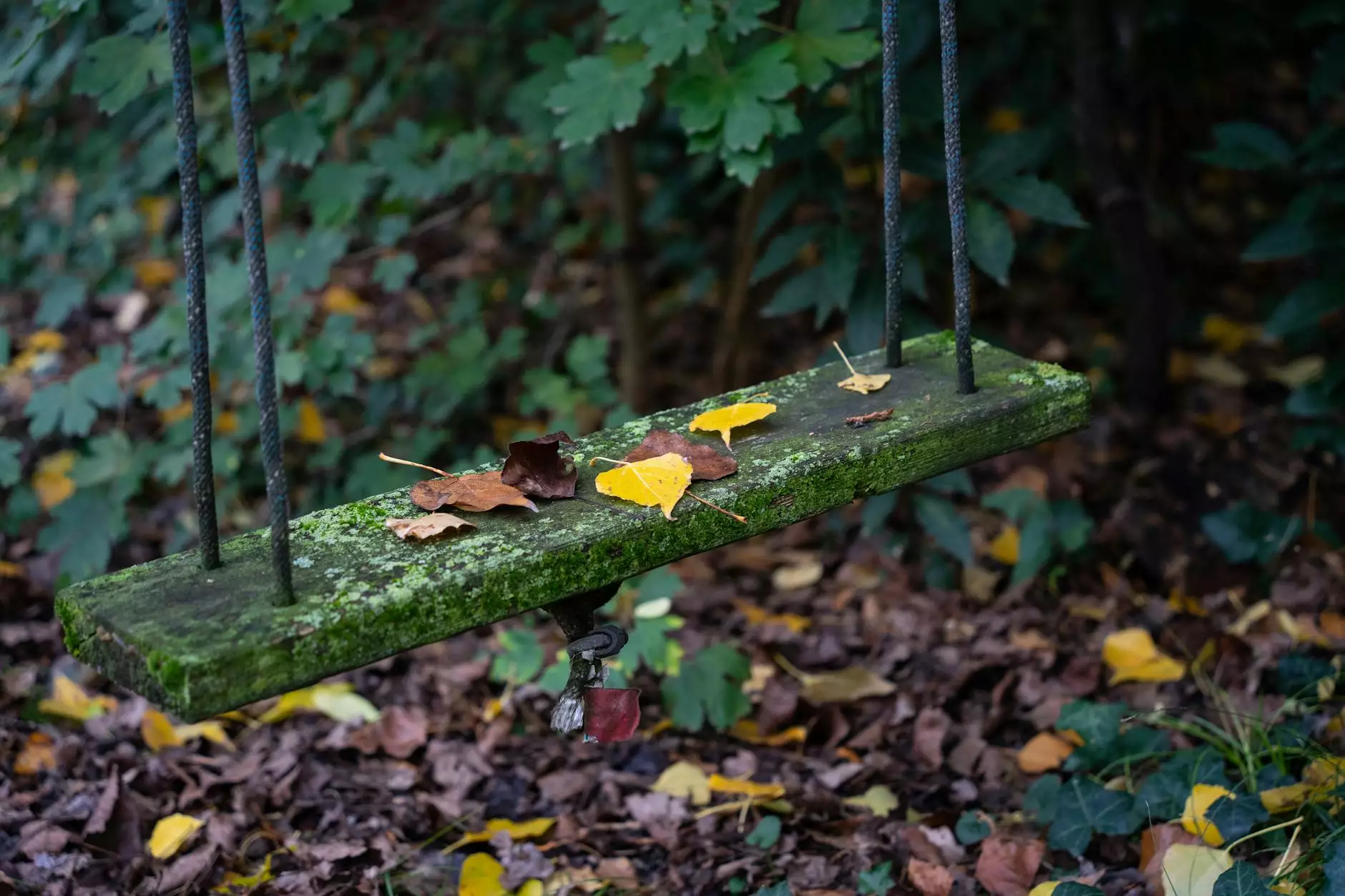
In today's ever-evolving industrial landscape, plastic molding manufacturing stands tall as a cornerstone of production efficiency and innovation. From consumer products to automotive parts, the versatility of molded plastics continues to revolutionize the way goods are produced and consumed.
What is Plastic Molding Manufacturing?
Plastic molding manufacturing involves several processes that transform raw plastic materials into finished products. It encompasses a variety of techniques, primarily focusing on shaping the plastic through the application of heat and pressure. The most common methods include:
- Injection Molding: This is the most widely used plastic molding technique, ideal for producing large quantities of parts defined by intricate designs.
- Blow Molding: Utilized for hollow plastic products, this method involves inflating a heated plastic tube to form bottles, containers, and more.
- Rotational Molding: This technique is perfect for making large, hollow parts by rotating a mold filled with plastic resin until it uniformly coats the inside.
The History of Plastic Molding
The origins of plastic molding can be traced back to the early 20th century. The first synthetic plastic, Bakelite, was invented in 1907 by Leo Baekeland and marked the beginning of an era where plastics became a viable alternative to traditional materials. Over the decades, advancements in technology and material sciences have drastically improved plastic molding techniques, making them more efficient and environmentally friendly.
Key Benefits of Plastic Molding Manufacturing
Adopting plastic molding manufacturing offers several advantages that enhance production processes:
- Cost-Efficiency: Once the molds are created, the cost of each subsequent piece is minimal, making it economical for mass production.
- Design Flexibility: The ability to create complex shapes and designs that would be difficult, if not impossible, with traditional manufacturing methods.
- Durability: Products made from molded plastics are often stronger and more durable compared to those created from other materials.
- Reduced Waste: Modern molding processes are designed to minimize scraps and waste, contributing to more sustainable manufacturing.
Understanding Different Types of Plastics Used in Molding
Plastic molding manufacturing typically involves the use of various types of plastics, each with its unique properties:
- Polypropylene (PP): Known for its elasticity and impact resistance, PP is widely used in automotive, packaging, and consumer goods.
- Polyethylene (PE): Common for its chemical resistance, PE is commonly used in producing containers, toys, and packaging materials.
- Polyvinyl Chloride (PVC): Renowned for its durability and cost-effectiveness, PVC is frequently used in construction materials and piping.
- Acrylonitrile Butadiene Styrene (ABS): This strong plastic is often utilized in making durable and impact-resistant products like automotive parts and household goods.
Applications of Plastic Molding Manufacturing
Plastic molding manufacturing finds its applications across various industries, showcasing unparalleled versatility:
1. Automotive Industry
The automotive sector relies heavily on plastic molded components such as dashboards, panels, and bumpers, contributing to weight reduction and fuel efficiency.
2. Consumer Goods
From household appliances to toys, molded plastics define the consumer goods industry, providing cost-effective and customizable solutions.
3. Medical Devices
In the medical field, precision and hygiene are paramount. Plastic molding ensures that medical devices meet stringent standards through tailored design and materials.
4. Packaging
The packaging industry has embraced molded plastics for their lightweight and durable properties, enhancing product protection while minimizing environmental impact.
Challenges in Plastic Molding Manufacturing
While the benefits of plastic molding are substantial, several challenges must be addressed:
- Initial Tooling Costs: Developing molds can be expensive and time-consuming, often posing a barrier for small manufacturers.
- Material Limitations: Not all plastics are suitable for every application, which necessitates careful material selection.
- Environmental Concerns: The impact of plastic waste on the environment remains a critical issue, prompting the industry to seek sustainable alternatives.
Future Trends in Plastic Molding Manufacturing
As industries evolve, so too does plastic molding manufacturing. Several trends are shaping its future:
- Advanced Materials: The development of biodegradable and recyclable plastics is paving the way for more sustainable production practices.
- Automation: The incorporation of robotics and artificial intelligence into production lines is enhancing efficiency and reducing labor costs.
- 3D Printing Integration: The convergence of 3D printing and plastic molding allows for rapid prototyping and customization, significantly speeding up the design process.
Choosing the Right Plastic Molding Partner
Finding a reliable partner for your plastic molding manufacturing needs is crucial for your business’s success. Here are some tips:
- Experience: Look for a company with a proven track record in your specific industry.
- Technological Capabilities: Ensure that your partner utilizes the latest technology and machinery to produce high-quality parts.
- Sustainability Practices: A partner committed to sustainable practices can enhance your own company's environmental goals.
- Customer Service: Strong communication and reliable support are essential for addressing any emergencies or changes in production.
Conclusion
The world of plastic molding manufacturing is rich with potential and innovation. As businesses navigate challenges and embrace emerging trends, the importance of efficient, sustainable practices becomes increasingly evident. Whether you're in the automotive, medical, or consumer goods sector, understanding the complexities and benefits of plastic molding can offer a significant competitive edge. Embrace the future of manufacturing with a partner that understands your needs and aligns with your vision for excellence.
To learn more about our plastic molding capabilities and how deepmould.net can assist you in your next project, feel free to contact us today!